La soldadura es un proceso de fabricación en donde se realiza la unión de dos piezas de un material, metales o termoplásticos normalmente, usualmente logrado a través de la fuson, en la cual las piezas son soldadas fundiendo, se puede agregar un material de aporte,que al fundirse forma un charco de material fundido entre las piezas a soldar, el baño de soldadura y, al enfriarse, se convierte en una unión fija a la que se le denomina cordón.
La soldadura puede ser hecha en muchos ambientes diferentes, incluyendo al aire libre, debajo del agua y en el espacio. Sin importar la localización, sin embargo, la soldadura sigue siendo peligrosa, y se deben tomar precauciones para evitar quemaduras, descarga eléctrica, humos venenosos, y la sobreexposición a la luz ultravioleta.
Soldadura heterogenia: es la realizada entre materiales de naturaleza diferente, independiente mente de que se aporte o no material, o entre mismos materiales pero con material de aportacion diferente.
Soldadura homogenea: los materiales a soldar son de la misma naturaleza, al igual que el material de aportacion en caso de haberle. Si no hay aportacion de material la soldadura se denomina autogena.
SMAW: También conocida como soldadura por arco eléctrico por electrodo prerevestido, se caracteriza, por la creación y mantenimiento de un arco eléctrico entre una varilla metálica llamada electrodo, y la pieza a soldar. El electrodo recubierto está constituido por una varilla metálica a la que se le da el nombre de alma o núcleo, generalmente de forma cilíndrica, recubierta de un revestimiento de sustancias no metálicas, cuya composición química puede ser muy variada, según las características que se requieran en el uso. El revestimiento puede ser básico, rutílico y celulósico. Para realizar una soldadura por arco eléctrico se induce una diferencia de potencial entre el electrodo y la pieza a soldar, con lo cual se ioniza el aire entre ellos y pasa a ser conductor, de modo que se cierra el circuito. El calor del arco funde parcialmente el material de base y funde el material de aporte, el cual se deposita y crea el cordón de soldadura.

Plasma: está compuesto por electrones que transportan la corriente y que van del polo negativo al positivo, de iones metálicos que van del polo positivo al negativo, de átomos gaseosos que se van ionizando y estabilizándose conforme pierden o ganan electrones, y de productos de la fusión tales como vapores que ayudarán a la formación de una atmósfera protectora. Esta misma alcanza la mayor temperatura del proceso.
Llama: es la zona que envuelve al plasma y presenta menor temperatura que éste, formada por átomos que se disocian y recombinan desprendiendo calor por la combustion del revestimiento del electrodo. Otorga al arco eléctrico su forma cónica.
Baño de fusión: la acción calorífica del arco provoca la fusión del material, donde parte de éste se mezcla con el material de aportación del electrodo, provocando la soldadura de las piezas una vez solidificado.
Cráter: surco producido por el calentamiento del metal. Su forma y profundidad vendrán dadas por el poder de penetración del electrodo.
Cordón de soldadura: está constituido por el metal base y el material de aportación del electrodo, y se pueden diferenciar dos partes: la escoria, compuesta por impurezas que son segregadas durante la solidificación y que posteriormente son eliminadas, y sobre el espesor, formado por la parte útil del material de aportación y parte del metal base, la soldadura en sí.
Electrodos: son varillas metálicas preparadas para servir como polo del circuito; en su extremo se genera el arco eléctrico. En algunos casos, sirven también como material fundente. La varilla metálica a menudo va recubierta por una combinación de materiales que varían de un electrodo a otro.

MIG/MAG: También conocida como semiautomatica, La soldadura MIG/MAG es un proceso de soldadura por arco bajo gas protector con electrodo consumible, el arco se produce mediante un electrodo formado por un hilo continuo y las piezas a unir, quedando este protegido de la atmosfera circundante por un gas inerte, MIG o por un gas activo, MAG.

La soldadura MIG/MAG es intrinsecamente mas productiva que la soldadura MMA donde se pierde productividad cada vez que se produce una parada para reponer el electrodo consumido. El uso de hilos solidos e hilos tubulares han aumentado la eficiencia de este tipo de soldadura hasta el 80%-95%. La soldadura MIG/MAG es un proceso versatil, pudiendo depositar el metal a una gran velocidad y en todas las posiciones, este procedimiento es muy utilizado en espesores pequeños y medios en estructuras de acero y aleaciones de aluminio, especialmente donde se requiere una gran trabajo manual. Presenta grandes ventajas, como no dejar escoria y su versatilidad, dado que se puede soldar en todas las posiciones.
Para obtener los mejores resultados en el proceso, es necesario conocer el efecto de cada variable sobre las diversas características o propiedades del proceso de soldadura. Algunas de estas variables, a las que denominamos variables preseleccionadas son:
Diámetro del alambre-electrodo
Composición química del mismo
Tipo de gas
Caudal
Por otra parte también hay que definir otras variables las cuales las denominamos variables primarias que son las que controlan el proceso después que las variables preseleccionadas fueron seleccionadas, estas controlan la estabilidad del arco, el régimen de soldadura y la calidad de la soldadura, estas variables son:
Tensión del arco
Corriente de soldadura
Velocidad de avance
Otras variables a tener en cuenta son las denominadas variables secundarias, que pueden ser modificadas de manera continua, son a veces difíciles de medir con precisión y especialmente en soldadura automática, estas no afectan directamente a la forma del cordón, pero actúan sobre una variable primaria que a su vez influye en el cordón. Estas variables son:
Altura de la boquilla
ángulo de la boquilla
Velocidad de alimentación del alambre
Los parámetros regulables que podemos considerar como más importantes y que más afectan a la soldadura son:
Polaridad
Tensión de arco
Velocidad del hilo
Naturaleza del gas
La soldadura por puntos es un método de soldadura por resistencia que se basa en presión y temperatura, en el que se calienta una parte de las piezas a soldar por corriente eléctrica a temperaturas próximas a la fusión y se ejerce una presión entre las mismas. Generalmente se destina a la soldadura de chapas o láminas metálicas, aplicable normalmente entre 0,5mm y 3mm de espesor.
El soldeo por puntos es el más dificil y complicado de los procedimientos de soldadura por resistencia. Los materiales bases se deben disponer solapados entre electrodos, que se encargan de aplicar secuencialmente la presión y la corriente correspondiente al ciclo produciendo uno o varios puntos de soldadura.
Es un tipo de soldadura que se cataloga por soldadura sin fusión del metal base a soldar, se considera un proceso en el cual los electrodos utilizados no son consumibles, además no se necesita material de aporte para que se produzca la unión entre las dos piezas, se considera un tipo de soldadura rápida, limpia y fuerte.
El material utilizado de los electrodos es una aleación de cobre con Cd, Cr, Be, W con objeto de que presente una baja resistencia y una elevada oposición a la deformación bajo una presión estando su dureza comprendida entre 130 y 160 HB.
También este tipo de soldadura necesita de un transformador donde la bobina secundaria suministra un voltaje a los electrodos de 1V a 10V y una gran corriente, debido a que generalmente la resistencia de las piezas a soldar es muy baja por tanto la corriente que debe pasar por la zona a soldar debe de ser del orden de los 500 amperios.
1. Intensidad-tiempo de soldadura
2. Resistencia eléctrica de la unión
3. Presión de apriete
4. Geometría de los electrodos
TIG (Tungsten Inert Gas): Muy utilizada para soldar acero inoxidable, se caracteriza por el empleo de un electrodo permanente de tungsteno, aleado a veces con torio o zirconio en porcentajes no superiores a un 2%. Dada la elevada resistencia a la temperatura del tungsteno (funde a 3410 °C), acompañada de la protección del gas, la punta del electrodo apenas se desgasta tras un uso prolongado. Los gases más utilizados para la protección del arco en esta soldadura son el argón y el helio, o mezclas de ambos.La gran ventaja de este método de soldadura es, la obtención de cordones más resistentes, más dúctiles y menos sensibles a la corrosión que en el resto de procedimientos, ya que el gas protector impide el contacto entre el oxígeno de la atmósfera y el baño de fusión. Además, dicho gas simplifica notablemente el soldeo de metales ferrosos y no ferrosos, por no requerir el empleo de desoxidantes, con las deformaciones o inclusiones de escoria que pueden implicar
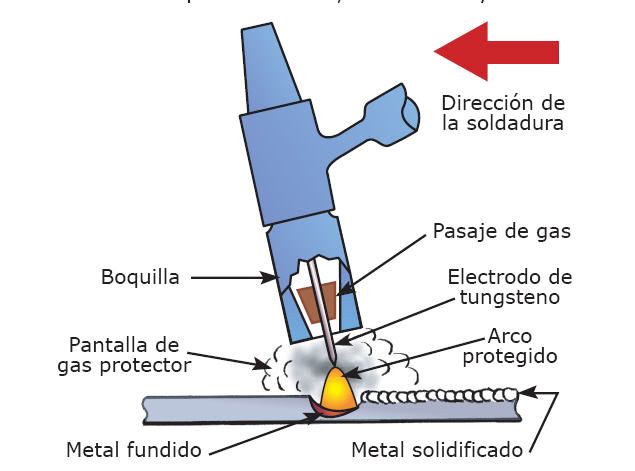
Soldadura por Laser: Muy utilizada en la producción en cadena de vehículos, la soldadura por rayo láser (LBW, de laser-beam welding) es un proceso de soldadura por fusión que utiliza la energía aportada por un haz láser para fundir y recristalizar el material o los materiales a unir, obteniéndose la correspondiente unión entre los elementos involucrados. En la soldadura láser comúnmente no existe aportación de ningún material externo. La soldadura se realiza por el calentamiento de la zona a soldar, y la posterior aplicación de presión entre estos puntos. De normal la soldadura láser se efectúa bajo la acción de un gas protector, que suelen ser helio o argón.

Mediante espejos se focaliza toda la energía del láser en una zona muy reducida del material. Cuando se llega a la temperatura de fusión, se produce la ionización de la mezcla entre el material vaporizado y el gas protector (formación de plasma). La capacidad de absorción energética del plasma es mayor incluso que la del material fundido, por lo que prácticamente toda la energía del láser se transmite directamente y sin pérdidas al material a soldar.
La elevada presión y elevada temperatura causadas por la absorción de energía del plasma, continúa mientras se produce el movimiento del cabezal arrastrando la "gota" de plasma rodeada con material fundido a lo largo de todo el cordón de soldadura.

La soldadura por soplete es uno de los procedimientos de soldadura fuerte más utilizados. Es muy utilizado en volúmenes de producción pequeños o en operaciones especializadas. Hay varias clases de soldadura por soplete, manual, semiautomática y automática.
Operario soldando con soplete
En la soldadura manual el operario se encarga de manejar el soplete y de colocar las piezas para su unión así como el material fundente. Se utiliza en procesos de bajo volumen o en los que una máquina operaría con dificultades. Su principal inconveniente radica en la habilidad del operario para realizar la soldadura.
La soldadura automática se caracteriza por eliminar casi por completo la necesidad de mano de obra humana para la realización de la soldadura, salvo para cargar y descargar las piezas de unión. Se usa para altos niveles de producción y para conseguir acabados mejores.
La soldadura semiautomática es una mezcla de la manual y la automática. En este tipo de soldadura es la máquina la que maneja el soplete mientras que el operario coloca los elementos a unir el fundente. Este proceso tiene como ventajas la reducción de la mano de obra y el hecho de que no es influyente la habilidad del operario para soldar.
